Collect. Connect. Convert.
Harnessing The Power Of Your Data Through explore the creation our AI repository for high quality information
Bumi Data Mining is the exclusive partner of VROC AI: a Software as a Service (SaaS) Platfom as a Service (PaaS) Automated Machine Learning (AutoML) platform, specifically designed and built for Industrial Big Data. BDM VROC AI is built to seamlessly integrate with your existing infrastructure and used by your existing team to quickly build, train, and maintain models of your asset without programming or coding experience.
Collect. Connect. Convert.
Harnessing The Power Of Your Data Through explore the creation our AI repository for high quality information
Bumi Data Mining is the exclusive partner of VROC AI: a Software as a Service (SaaS) Platfom as a Service (PaaS) Automated Machine Learning (AutoML) platform, specifically designed and built for Industrial Big Data. BDM VROC AI is built to seamlessly integrate with your existing infrastructure and used by your existing team to quickly build, train, and maintain models of your asset without programming or coding experience.
Using AI To Predict Turbine Compressor Failure
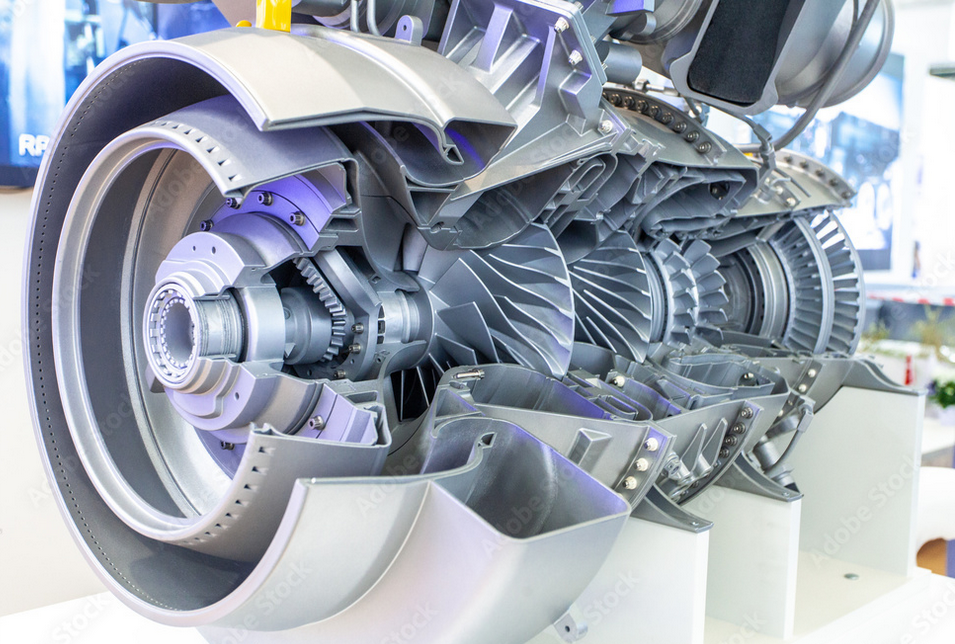
AI raises alarm for Turbine Compressor failure, identifying the root cause as an oil leakage issue
- One of BDM’s clients is a National Oil and Gas operator. Their off-shore platform is equipped with two primary Turbine Compressors operating in parallel. The client wanted to predict potential undesirable performance and reliability issues, so that they could intervene early to avoid shutdowns.
- The BDM VROC AI is used by the oil and gas platform, with real time operational data from across the whole plant being continually ingested. The client’s Subject Matter Expert, generated a Time to Failure (TTF) AI model on the BDM VROC platform for Turbine Compressor #2 (TC2), to predict undesirable performance. This TTF model was trained in order to predict potential Turbine Compressor undesirable performance, using the Turbine Compressor’s speed as the target. This model is generated in order to get early warning detection when turbine rotational speed (NGP) is about to reduce below than 8000 rpm.
- Based on the features introduced to the model, the model established a strong relationship with one of the features known as LUBE OIL RESERVOIR LEVEL (shown below). The model raises a warning every time the lube oil level reduces and requires top up. Such behaviour was not observed in the other turbine compressor. However, the model warnings are reduced after the Operation team has rectified the coupling cover & tightened the connections.
- The models have shown the top contributor for the failure of Turbine Compressor #2 on high speed is the lube oil tank level. After rectifying the major lube oil leaking issue, it’s performance has improved. The client’s team are now closely monitoring the lube oil level, topping up whenever necessary to ensure continued reliability.
- This is one of several recent ‘catches’ by the Oil and Gas Plant Operators using the no-code AI platform. These insights are helping the client prevent unplanned downtime, and improve production on their offshore platform.